Advanced Manufacturing in Singapore and Arcstone's Role - MONEY FM89.3 Interview
- Willson Deng
- Jul 29, 2021
- 7 min read
On MONEY FM89.3 Breakfast Huddle, Arcstone’s CEO Willson Deng shared with the host, Elliott Danker on the advanced manufacturing space in Singapore now and Arcstone's mission and efforts during COVID-19.
Elliott: I’d like to start off first by trying to understand your company Arcstone – I know it’s an experienced and dedicated software company, but what else can you tell us?
Willson: Exactly, Arcstone is a digital manufacturing solutions provider. We provide toolsets to run the shop floor and operations on the factory level, connecting the entire supply chain end-to-end. Our focus is on providing tools that make it easy for users to take on the toolset to digitize and go paperless in the shop floor, to ensure you can see the production process is being run, no matter where you are in the world.
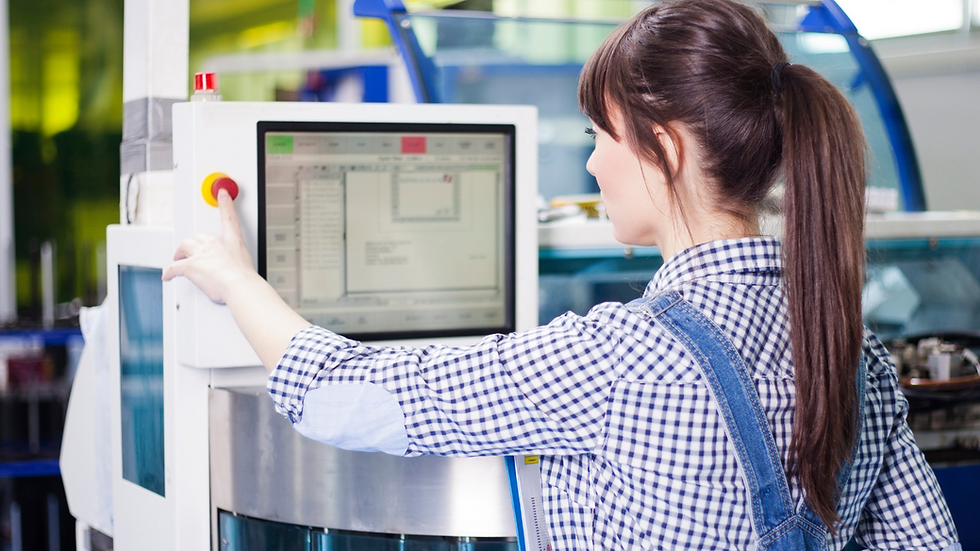
E: So, what you're saying is that you can simplify all of this simply with data?
W: The core thing that Arcstone is trying to move here is that data is what makes it better. Having that visibility, having that transparency and being able to operationalize that data when it's coming in to make better decisions. It is a difficult thing to perform while you're transitioning. A lot of the old ways of doing work, which were paper-and-pencil, used to be something that people used when operating on the shop floor – they now need to convert this into a toolset that can scale and be taught to the next generation and can bring about additional value.
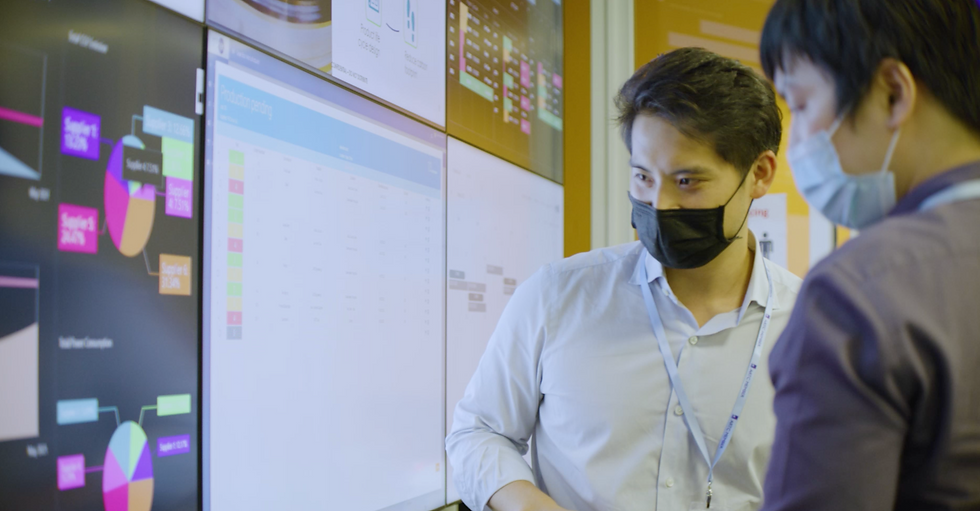
E: What are some of the pain points that SMEs in the manufacturing sector are facing when they are trying to go digital?
W: It’s not an easy process despite an uptick in manufacturing operations so far. Despite the COVID situation, it's still a daunting task to have to transform a traditional operation that they have been running in a similar way for the past couple decades.
Now, having to take on new tools – that's a lack of talent, of people capable of helping out with these digital understandings – and to be able to transform [processes], but [not having] the digital touch and having to update and transform that kind of mindset is definitely not easy.
On top of great solutions, craftsmen are needed – to be able to take up these tools, leverage it, work on it, and [take] action on it when the data starts coming in, and that's something where education is a very critical part.

E: If I were to engage Arcstone, how will Arcstone implement the solutions, and will you provide training for staff?
W: In order for us to get going and to remove as many barriers from the shop floor and for SMEs in general, we have a toolset called arc.lite, which is completely free, unlimited, and for anyone to use with no restrictions and expiry date. It’s designed to help SMEs go fully digital, with no upfront cost, designed to achieve a paperless operation – directly running on shop floor, and move everything that used to be done in paper-and-pencil into this particular digital tool.
Arcstone is also working very closely with institutes of higher learning, for example, students from NUS in their master's degree program. We provide these toolsets to students for them to learn how to use digital tools, a digital manufacturing execution system.
Another example is Temasek Polytechnic – we had the opening of their advanced manufacturing centre last month, and again this is the same process of bringing these tools, not just to the institutes of higher learning, but getting them into the actual factories, getting students involved with the SMEs so that there's a helping hand and for them to immediately become the next potential hires as well. It's the cycle that Arcstone is trying to grow, not just the solution, but how do we build this kind of supportive ecosystem to encourage SMEs to adopt, but know that they will have the HR backing behind them, and the talent pool ready to support these tools when they come onboard.
E: What’s the current state of advanced manufacturing here in Singapore?
W: A very vibrant space, a lot of companies are driving a lot of fantastic solutions in this space, but one of the key, perhaps the hindrances for this to move even further, is indeed this lack of this talent pool. There's a lot of interest – software development digital tools, mechanical engineering, etc – but they end up going into different fields. A lot of the younger generation don't realise how advanced manufacturing has really moved.
One of the things that we have done a lot with is trying to attract students and the next generation to the advanced manufacturing technology space. Facilities are now using the latest technology e.g. AGVs going around, cobots, advanced intelligence and machine learning tools, and industrial IoT tools. It is a very different environment from what people typically think of the “old-school” kind of manufacturing operations.
This is truly the advanced digital space, and hopefully what we're trying to do now is to work with more of these institutes of higher learning, to bring in these kinds of use cases, these demonstration centres, these learning centres to get people to realize that this is what's lacking, this is what we need a lot more of. If you have talent in place, there comes more innovation, more implementation, more utilization of these types of tools.
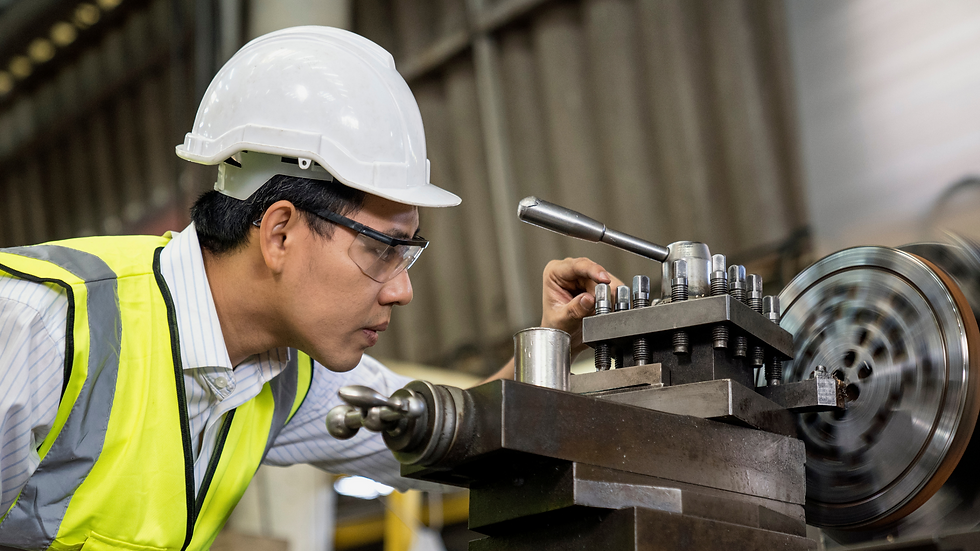
E: Has COVID-19 shifted the mindset towards digitalization, especially with the lack of talent that we saw before that, or are people learning about it but just not sticking to that field, do people feel or has their mindset changed because of COVID-19?
W: Absolutely, because of COVID-19, people realized they couldn’t set foot into factories anymore because of COVID regulations, or couldn't fly out and visit overseas factories anymore.
People will start to think how they are going to manage and run processes, with a growing talent pool that is not interested in always working in a factory setting but wants to move into the digital space or want to move into more advanced functionalities and development work. So, you have a lack of workers in general.
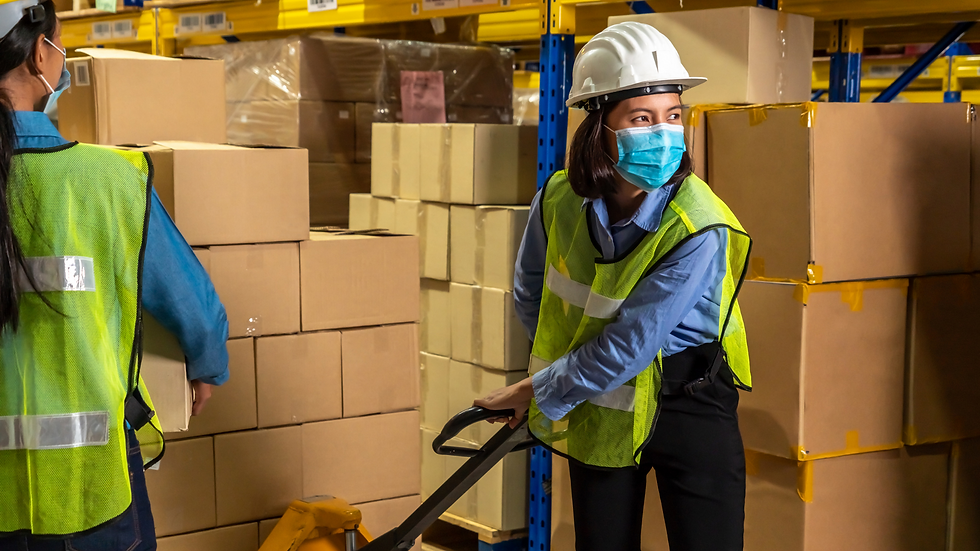
Looking at digitalization to maximize the value and having direct transparency over processes becomes fundamental and essential, not just for making sure that you maintain and continue operations, but the information that is now needed for the rest of the supply chain.
Most manufacturers provide parts and components and critical features and solutions to the larger multinationals of this world, and if you are not able to now provide real-time, live, validated data to prove the quality control and the output, they're going to start looking for other options elsewhere. It's a very competitive environment, so the need to digitalize or face the risk of missing out is a very big condition that everyone needs to realize.
E: Tell us more about the $18 million joint lab with A*STAR
W: It’s a very fantastic moment for Arcstone as we open this joint lab, we’re focused on four key research streams:
1. Vision systems to overseas operations on the shop floor, easily and quickly
2. Machine and human integrations, allowing for drag and drop machine programming
3. Scheduling procedures, how do we optimize the entire production process from shop floor and connect that across the supply chain for all the other players that are in the ecosystem to get that final product produced
4. Bringing sustainability into the manufacturing space in a way that allows for users to look at sustainability, not as a cost factor, but to be able to measure it and use it as a competitive advantage.
A lot of manufacturing is a reactive process to consumers in this space, where we're seeing a lot of the consumer demand – consumers are realizing that every single thing that they buy has an impact on the earth – as they become more relevant and aware of that particular impact, it makes them change their particular buying preferences, and in which case manufacturers need to quickly adjust and approve.
These tools that we're coming out with, especially on the sustainability side, are to make sure that they become democratized, it's not just a black box where only the engineers understand, but to move all these tools into the hands of the SMEs so that any operator, any engineer, any programmer or developer or anyone that is on the ground, even traditional workers can adopt them quickly and start putting them into action.
E: The various collaborations you have with institutions – all these play a part in helping to supplement the lack of talent that we have seen in the past. What are your thoughts on how this will sustain and ensure that this talent pool grows?
W: This is part of the responsibility of Arcstone. If you look back at my personal side, from university and having the experience and the capability to have interned in a lot of different roles and factories – that has been a big driving factor in making me fall in love with this industry.
Digital manufacturing providers need to spend more time with the institutes of higher learning to bring about a change of mindset to open the eyes of students that may have gone for a different role or responsibility somewhere else. If they had only known what manufacturing is like, how advanced it has become, how there's such a demand for these particular types of skill sets, and the amount of impact that they can make in this industry, especially in the sustainability side of manufacturing, this is going to attract a lot of students.
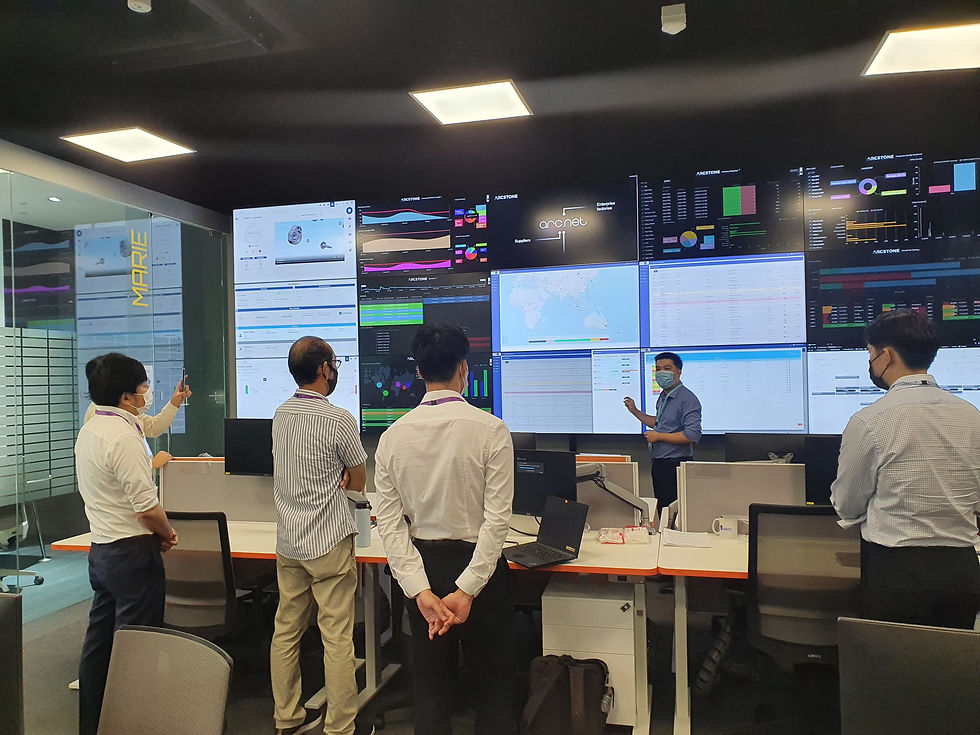
This will be a concentrated effort, it's not going to be something that'll be done overnight, but it's a year over year [push], along with continued. It’s a long-term investment from Arcstone’s standpoint. The internships that we offer, we would like to see them join us / the industry after they graduate. Every company that is looking into digital manufacturing advanced manufacturing now needs to invest into the educational system by providing their time, providing the solutions, and providing their capabilities to capture this talent and inform students of this field that has demand for these skillsets.
Listen to the full interview here: https://omny.fm/shows/money-fm-893/mind-your-business-the-state-of-advanced-manufactu#.YP4mx6RKWWg.link
Comentarios