Top Digital Initiatives You Should Consider as a Small Manufacturer
- Willson Deng
- Dec 9, 2020
- 2 min read
Updated: Jan 6, 2021

Shifts in the Manufacturing industry have sparked off a multitude of new and developing initiatives to cope with changing global demands. Here are some of the top key digital initiatives across different industries over the last few years:
1. Supply Chain Collaboration Use digital data to support the supply chain and to fill any information gaps. Eliminate data silos and bottlenecks, building track and trace capabilities and AI-enabled cognitive insights into supply chain.
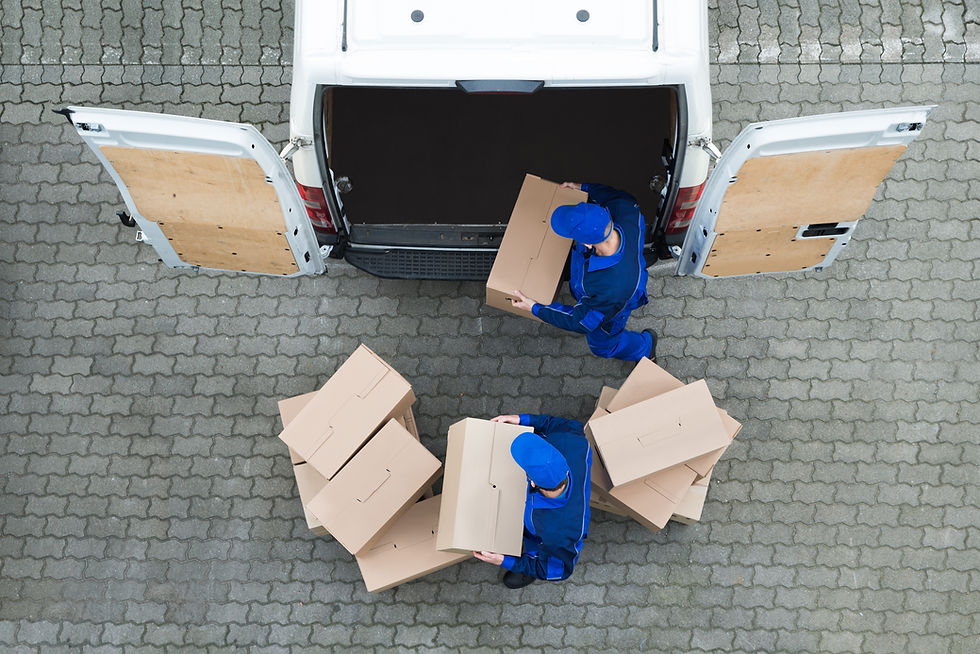
Company 1 wants to improve delivery time but does not know what part of the process needs improvement. By digitalizing part of their supply chain process, they are able to find the source of problems and predict which areas will need help in the future.
2. Digitalization of Manual/Paper Processes
Get rid of user errors such as version control, misplacement, and simply losing the paper. By digitalizing, access can be granted immediately, utilized remotely and never irreplaceable.
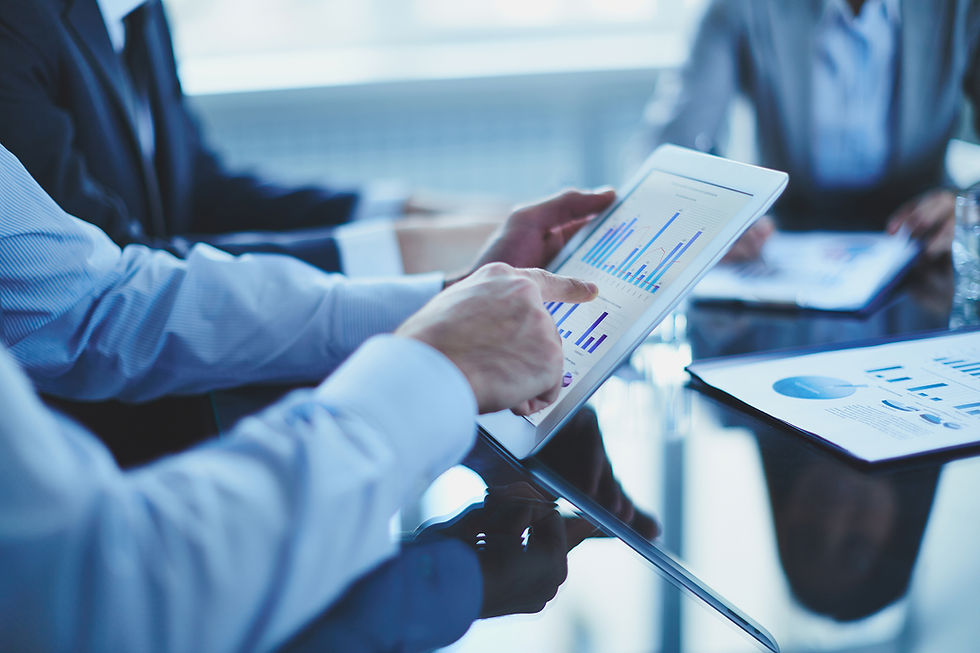
Company 2 uses detailed paper checklists to maintain their machines every day. After checking the machines, the engineers take 20 minutes to manually enter the details of the checklist to an Excel sheet. Every few months a new version is made and it is difficult to keep track of the most updated checklist. After digitalizing their paper processes, the engineers at Company B always know which version of the checklist is the most updated and no longer have to manually enter in the data.
3. Efforts to Implement Robotics and Automation
Many employees may think that robotics and automation are taking over their jobs. However, implementing these new technologies “enable employees to focus on innovation, efficiency and other, more intricate processes that ultimately lay the groundwork for growth and success.” (Source: Robotics in Manufacturing, Acieta LLC)
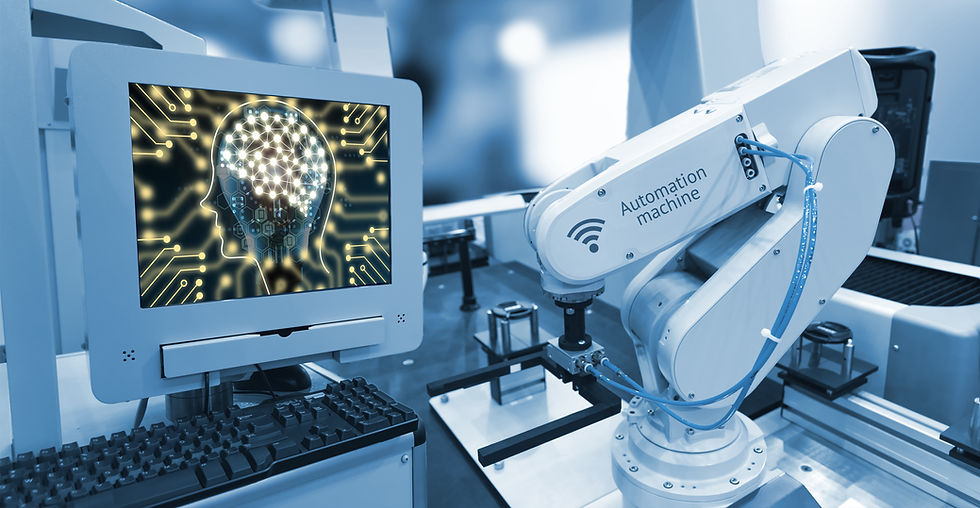
Company 3 wants to improve their efficiency. Their dyes machine has specific and detailed requirements between usage that can greatly impact production. Previously, managers would spend lots of time analyzing the most optimized order of customer orders to use the dyes machine. After implementing automation, production has been more efficient and the managers are able to spend more time solving other problem points.
4. Connection to Shop-Floor Sensors
Sensors on the factory floor can help monitor machine status, location of inventory and analyze new ways to improve production efficiency.

Company 4 has a lot of materials and wants to be better at keeping track of them. Previously, they only noted down the details on paper. Using RFID tags, scanners and shop-floor sensors, personnel can track where the material is, what step in production it is in, when it was last moved and who was the last person to handle it.
Curious to hear more about how we can help you get started on your digitalization journey in 1 day? Discover more here.
Comments